The footwear industry is an intricate web of design, material selection, and manufacturing processes. One critical aspect that often gets overlooked is the marking and bending processes, particularly the center of bend marks on mechanical and electric benders. This article delves into the significance of these marks, practical experiences, case studies, and tips for manufacturers.
What are Center of Bend Marks?
Center of bend marks are indicators used in the manufacturing process to denote the precise point where a shoe component will be bent or shaped. These marks are crucial for ensuring that the final product meets design specifications and maintains structural integrity. In the footwear manufacturing process, these marks serve multiple functions, including:
- Providing a reference point for accurate bending.
- Assisting in the alignment of different shoe components.
- Facilitating quality control measures.
Why are Center of Bend Marks Important?
In the production of customized footwear, especially where precision is paramount, knowing the exact location of bends can make a significant difference. Poorly marked centers often lead to:
- Misalignments of shoe components, resulting in poor fit.
- Weakened structural integrity of footwear, affecting durability.
- Increased production costs due to materials being wasted.
Types of Benders: Mechanical vs. Electric
Understanding the differences between mechanical and electric benders is essential for making informed decisions in footwear production. Both types have their pros and cons.
Mechanical Benders
Mechanical benders are commonly used in various manufacturing processes, including footwear. Here are some characteristics:
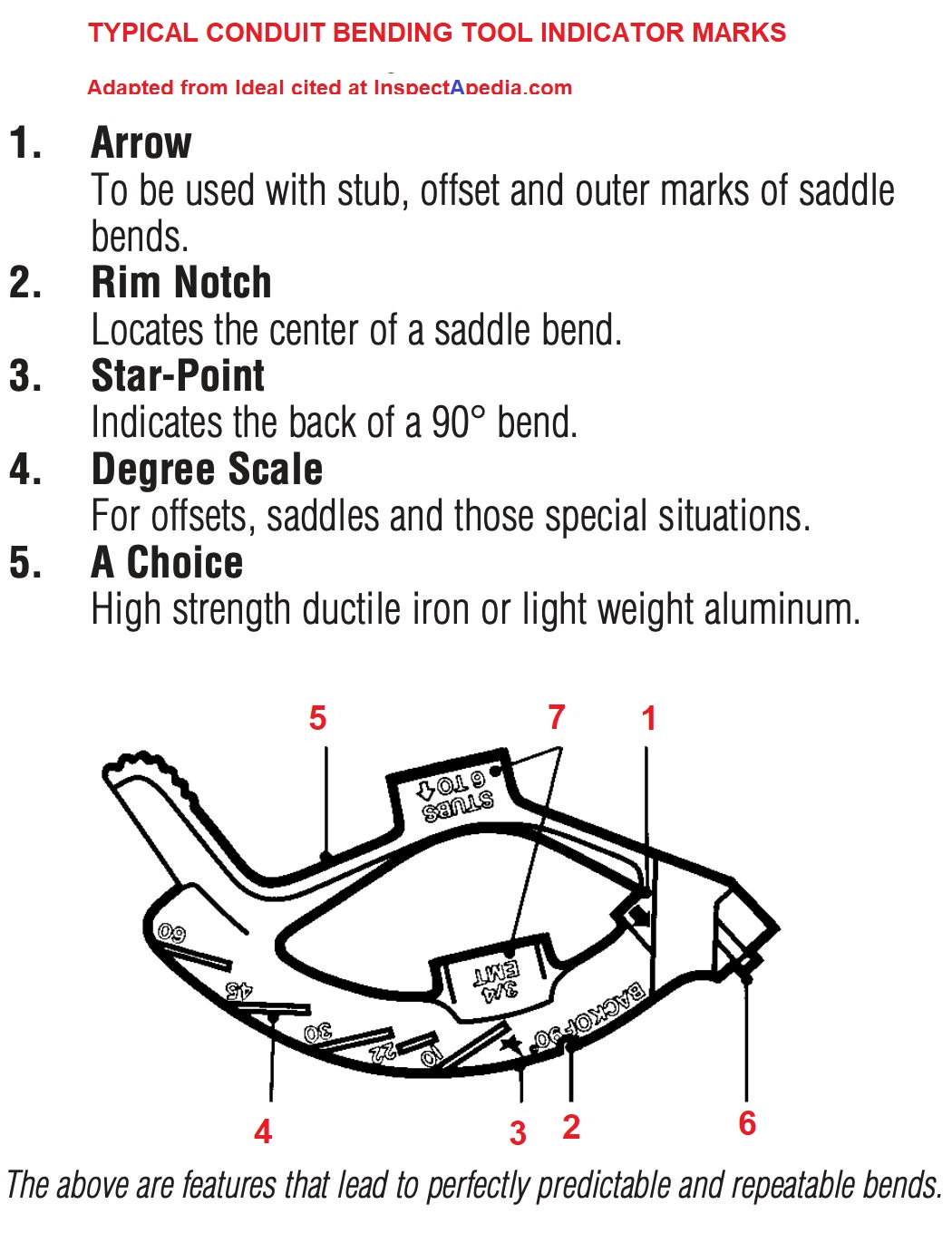
Advantages | Disadvantages |
---|---|
Cost-effective and easier to maintain. | Requires more physical effort to operate. |
Provide a high degree of control. | May have limitations in precision for complex designs. |
Electric Benders
Electric benders, on the other hand, offer advanced features that are particularly beneficial in a high-paced manufacturing environment. Here is a comparison:
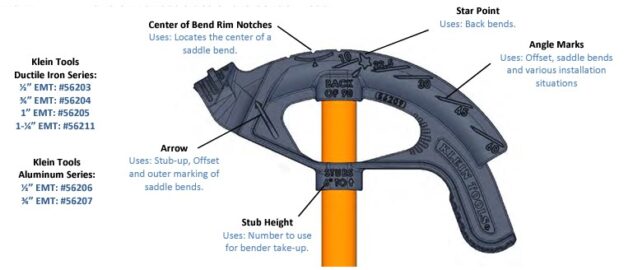
Advantages | Disadvantages |
---|---|
Higher precision and repeatability. | Higher initial investment cost. |
Faster operation speeds. | May require specialized training for operation. |
Real-World Footwear Experiences
To understand the practical applications of center of bend marks, let’s explore a case study of a renowned footwear brand that revamped its production process.
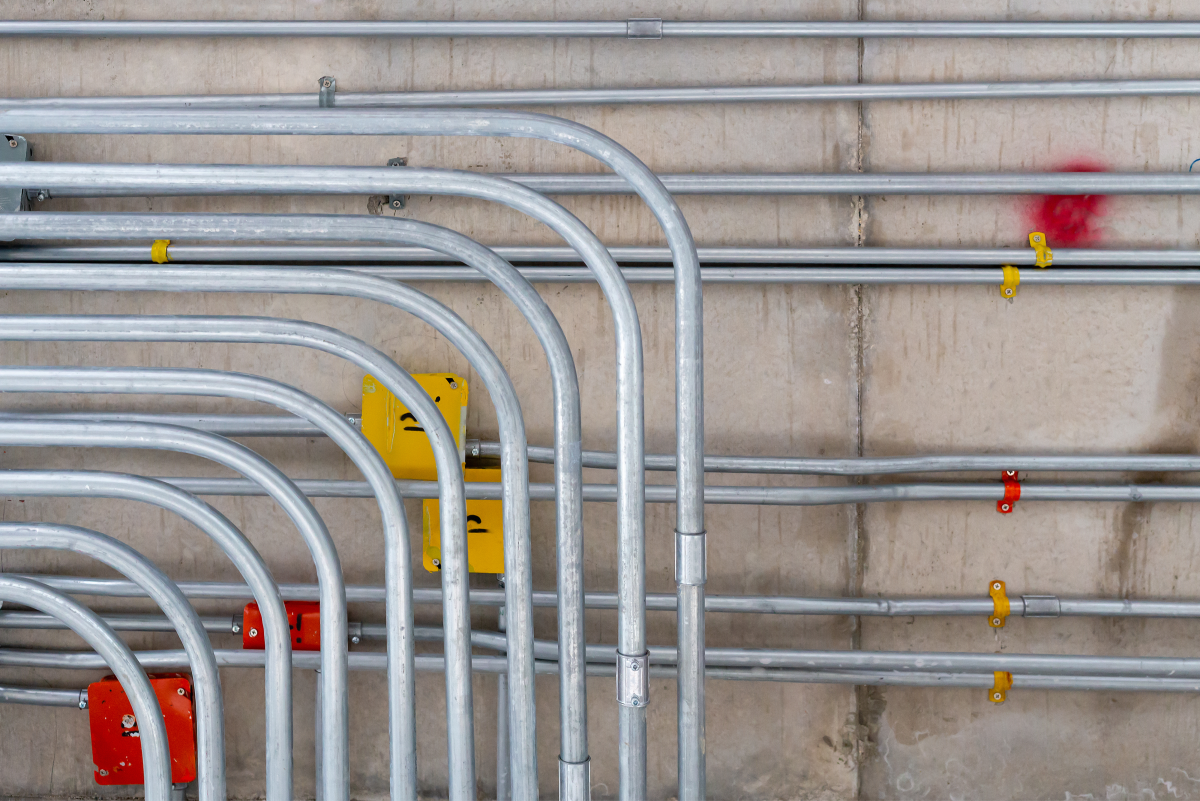
Case Study: XYZ Footwear
XYZ Footwear, a leader in sustainable shoe manufacturing, noticed an increase in production errors due to inaccurate bend marks on their mechanical benders. After analyzing their workflow, they found that improper markings were leading to a 20% increase in material waste.
To resolve this, they decided to invest in electric benders equipped with advanced laser marking technology for precision bend marking. As a result, they reported:
- A 30% reduction in material costs.
- An increase in employee satisfaction due to reduced manual labor.
- Improved overall product quality, leading to higher customer satisfaction.
Important Tips for Managing Bend Marks
1. Understanding Marks
Ensure that all team members are well-versed in interpreting the center of bend marks. Conduct regular training sessions to familiarize them with the machinery and its requirements.
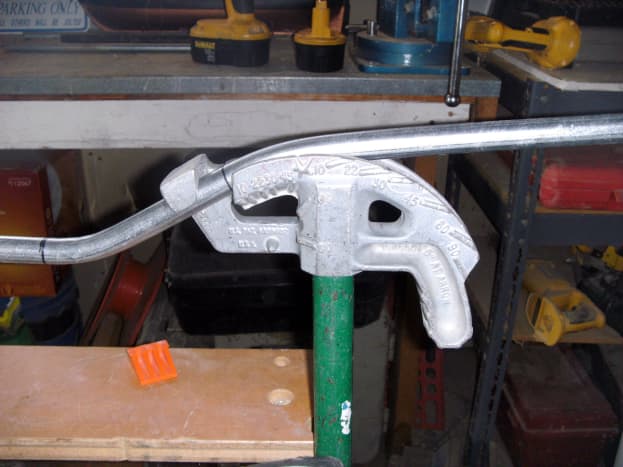
2. Quality Control Checks
Incorporate regular quality control checks in your production line to catch any misalignments early on. Utilize measuring tools to verify the accuracy of bend marks.
3. Optimize Workflows
Evaluate and optimize your workflows regularly. Identify bottlenecks and streamline processes to ensure that production runs smoothly and efficiently.
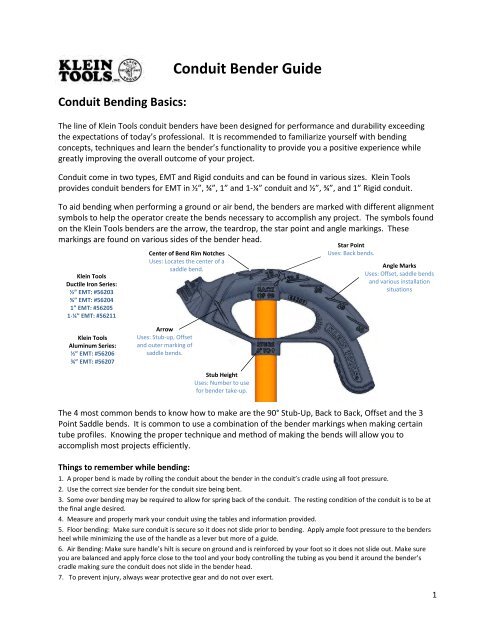
4. Seek Expert Consultation
If your production facility is experiencing consistent issues with bend marks, consider consulting an expert in footwear manufacturing processes. They can provide insights into best practices and technology upgrades.
Product Highlights and Recommendations
When considering upgrading to electric benders or investing in mechanical options, keep the following products in mind:
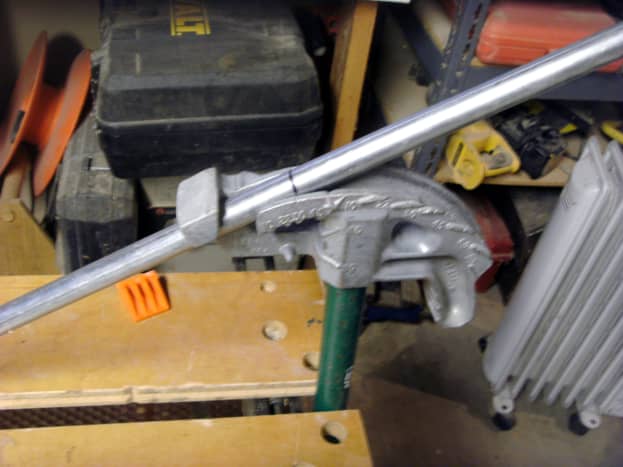
Top Electric Benders
- Brand A Electric Bender: Known for its precision laser marking and user-friendly interface.
- Brand B Heavy-Duty Electric Bender: Ideal for high-volume production with advanced safety features.
Top Mechanical Benders
- Brand C Mechanical Bender: Offers robust performance at an affordable price.
- Brand D Versatile Mechanical Bender: Suitable for various materials and shapes.

Pros and Cons of Using Center of Bend Marks
Pros
- Enhances accuracy in production.
- Facilitates smoother workflow in manufacturing processes.
- Reduces material waste and costs.
Cons
- Requires initial training and adaptation.
- Potential for errors if not properly implemented.
FAQs About Center of Bend Marks
1. What materials do center of bend marks work with?
Center of bend marks can be used with various materials, including leather, synthetic fabrics, and rubber, commonly used in footwear production.
2. How often should bend marks be checked?
Bend marks should be checked at the start of each production run and periodically throughout the process to ensure accuracy.
3. Can I use a mechanical bender for intricate designs?
While mechanical benders can be used for intricate designs, electric benders generally offer higher precision and are recommended for complex shapes.
4. What training is required for using electric benders?
Operators should receive comprehensive training covering machine setup, operation, safety protocols, and maintenance procedures.
5. Are there safety concerns with bend marking equipment?
Yes, safety concerns include mechanical hazards and electrical risks. Always adhere to safety guidelines and use appropriate personal protective equipment (PPE).
6. How do I know if I need to upgrade my bender?
If you frequently experience issues with bend accuracy or excessive waste, it may be time to consider upgrading your equipment.
7. What role does technology play in bend marking?
Technology, such as laser marking systems, significantly enhances precision and efficiency during the bending process, reducing the likelihood of errors.
8. Can I customize bend marks for my shoe designs?
Yes, many modern bender machines allow for customization of bend marks based on specific shoe designs and manufacturing needs.
9. How can I ensure quality control during production?
Implement regular audits, utilize digital measuring tools, and conduct training workshops for your team to ensure quality control in production.
Conclusion
Understanding the center of bend marks in mechanical and electric benders plays a vital role in the footwear manufacturing process. By investing time in training, optimizing workflows, and ensuring accurate marking, manufacturers can significantly enhance quality, reduce waste, and ultimately improve customer satisfaction. Whether you choose mechanical or electric benders, always prioritize precision and efficiency for the best results in your footwear production.